Le fabricant de fenêtres MéO décloisonne ses données
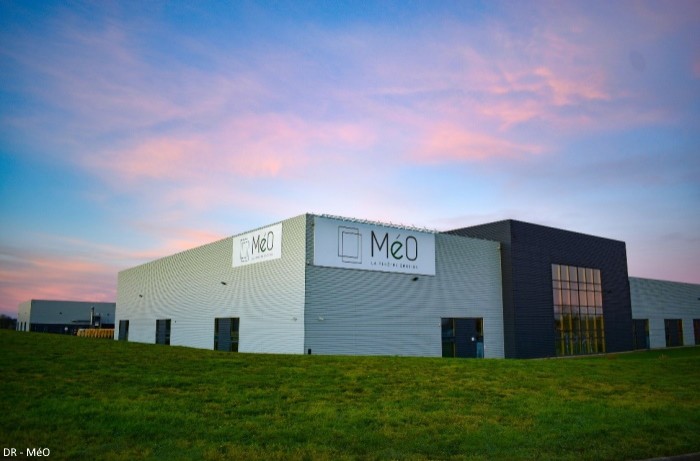
Le fabricant de fenêtres français MéO utilise les solutions de Magic Software pour décloisonner ses données, afin de gagner en agilité et de piloter sa production en temps réel.
PublicitéMéO est un fabricant de fenêtres français, spécialisé dans les menuiseries bois-aluminium sur mesure. Il fait partie du Groupe Liébot, une entreprise industrielle de 3000 employés qui est présente dans deux grands domaines d'activité, les fenêtres et les façades. En 2019, MéO a lancé un projet visant à décloisonner les données de son ERP. Pour cela, l'entreprise s'est appuyée sur la plateforme d'intégration Magic xpi, de Magic Software. Elle poursuit aujourd'hui cette démarche avec le déploiement du module de supervision Matics de FactoryEye, autre solution de l'éditeur destinée aux entreprises industrielles, dans le but de piloter en temps réel sa production.
Quand le projet a démarré, l'enjeu pour MéO était de renforcer la maîtrise de ses flux de données, de façon à pouvoir exploiter celles-ci plus aisément. « A l'époque, nous avions pour priorité de décloisonner notre ERP en sortant un certain nombre de données, notamment nos données techniques et clients, afin de regagner en agilité », explique ainsi Anthony Fèvre, responsable SI de MéO. Après avoir découvert la plateforme d'intégration et d'orchestration des flux Magic xpi, l'entreprise a décidé de la mettre en oeuvre, appréciant notamment sa flexibilité et son ouverture au niveau de la restitution des données.
Définir où sont les données maîtres
Une fois la décision prise, MéO a commencé par cartographier l'ensemble des flux existants au sein de ses applications, puis le fabricant a transféré ses données techniques et clients (gestion commerciale) au sein de logiciels métiers dédiés. L'entreprise a également mis en place des ateliers de travail afin de préparer l'intégration des différents flux de données, incluant celles de l'ERP et celles de son logiciel de pilotage de la production (MES). Grâce à deux sessions de formation organisées en interne, fin 2019 et début 2020, les équipes informatiques ont pu prendre la main sur la solution et devenir autonomes sur la plateforme. Durant ces sessions, les premiers flux relatifs aux données clients ont été déployés. « Les données clients sont partout, dans toutes nos applications, mais dans ce cas précis, nous avons décidé de donner la priorité à l'ERP en termes de mise à jour et de restitution. Cette nécessité de définir le sens des flux et où se situent les données maîtres est très importante : cela doit être effectué lors de chaque déploiement. C'est pourquoi il était important pour nous de pouvoir maîtriser la solution en interne et de faire appel aux consultants experts de Magic Software uniquement lors de nouveaux projets d'intégration », souligne Anthony Fèvre.
D'autres flux de données ont été mis en oeuvre par la suite, portant notamment sur les articles produits, les commandes, la gestion du cycle de vie de production et la gestion des livraisons. Toutefois, certains de ces flux ne sont pas encore en production, les solutions qu'ils sont destinés à alimenter ne l'étant pas encore.
PublicitéDes informations disponibles en temps réel
MéO a désormais entamé une nouvelle étape de son projet, visant à renforcer la circulation des données entre la production et les différentes briques de son système d'information, afin d'aller vers un pilotage de production en temps réel sur le modèle de l'industrie 4.0. Pour cela, il s'appuie sur le module de supervision Matics, rattaché à la solution FactoryEye de Magic Software. Le fabricant a demandé à l'éditeur de réaliser un Proof of Concept (POC) sur son activité fenêtres. « À l'issue de ce test, qui s'est déroulé entre janvier et avril 2021, nous sommes rentrés directement en phase de production sur un de nos sites, et ce, sur la base d'un contrat annuel en mode Saas », indique Anthony Fèvre. Depuis, le fabricant fait régulièrement évoluer la plateforme à travers des comités techniques hebdomadaires. Après un deuxième POC, réalisé en juillet 2021 au niveau du groupe, le fabricant a décidé de déployer la solution sur tous ses sites de production, soit une trentaine de machines-outils au total. « Aujourd'hui, nous avons une bien meilleure maîtrise de nos flux et disposons d'informations en temps réel qui nous sont très utiles pour optimiser nos lignes de production et améliorer nos performances. Nous avons aussi gagné en efficience collaborative, notre objectif étant à terme d'utiliser un seul et même portail d'entrée pour toutes les entités du groupe », conclut Anthony Fèvre.
Article rédigé par

Aurélie Chandeze, Rédactrice en chef adjointe de CIO
Suivez l'auteur sur Linked In,
Commentaire
INFORMATION
Vous devez être connecté à votre compte CIO pour poster un commentaire.
Cliquez ici pour vous connecter
Pas encore inscrit ? s'inscrire