Comment Petit Bateau a gagné une semaine sur son processus de planification
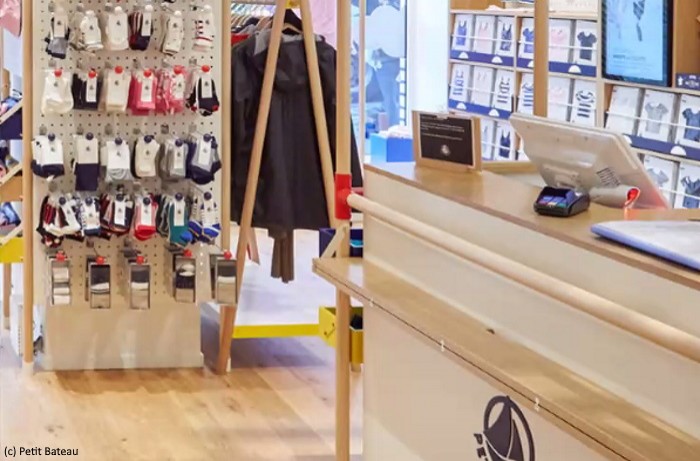
Lors d'un webinaire le 26 janvier, la marque de mode française Petit Bateau a présenté son projet OSCAR, qui a permis d'optimiser la planification de la production grâce à la mise en place de la solution FuturMaster.
PublicitéAppartenant au groupe Rocher, la griffe de mode française Petit Bateau, connue pour ses vêtements en maille, s'adresse à des clients de tous les âges, du bébé à l'adulte. Elle gère de ce fait un catalogue étendu, comptant 25 800 références coloris/tailles par an. Par ailleurs, l'entreprise fabrique elle-même 90% de ses produits, ce qui nécessite de gérer une supply chain complexe. Afin de gagner en agilité sur sa production, la marque a lancé en 2017 un projet d'optimisation de la planification, dénommé OSCAR (Objectifs Service Client, Agilité et Réactivité). Lors d'un webinaire organisé par FuturMaster le 26 janvier, Petit Bateau est revenu sur ce projet et sur les bénéfices obtenus.
« Nous sommes sur un marché textile en pleine évolution », lance en introduction Jean-Philippe Gauthier, directeur systèmes d'information métiers collection et opérations chez Petit Bateau. « La demande est de plus en plus internationale, le marché de la seconde main se développe tandis que les modèles de 'Fast Fashion' sont en perte de vitesse. Les clients désirent quant à eux de plus en plus d'instantanéité, ils sont en quête de sens et de valeurs, mais aussi de personnalisation et de services exclusifs. » Face à ces changements rapides, l'entreprise doit s'adapter, ce qui passe notamment par une stratégie industrielle à la fois responsable et agile. « Il s'agit de gagner en rapidité et en rentabilité, tout en réduisant notre empreinte environnementale et en travaillant sur la qualité, la durabilité et le recyclage », explique le DSI. Pour répondre à ces enjeux, la marque a engagé une réflexion afin d'optimiser sa chaîne d'approvisionnement. « Nous fabriquons environ 25 millions de pièces par an », indique le DSI. Cette production repose sur une supply chain complexe, avec plusieurs sites, mais aussi plusieurs métiers, allant du tricotage à la teinture en passant par la confection, la broderie ou la sérigraphie. La marque gère également plusieurs niveaux de nomenclature, et différentes volumétries au niveau des composants, des produits intermédiaires et des produits finis. Enfin, le secteur textile se caractérise par une forte saisonnalité, 90% des produits étant renouvelés tous les six mois. Dans ce contexte, la planification de la production joue un rôle essentiel pour répondre de façon efficace aux besoins des clients. « Ce processus intervient sur les niveaux tricotage, teinture et confection de nos sites de production », explique Christian Bouillot, responsable projets stratégiques chez Petit Bateau. « À partir du fil approvisionné, nous fabriquons les tricots, nous les assemblons et les coupons dans nos différents ateliers et ceux de nos partenaires, en France, au Maroc et en Tunisie. Enfin, dans certains cas nous assemblons également des produits finis pour composer des kits. »
PublicitéÉlaborer des plans de production exécutables
Afin de gagner en réactivité et en fiabilité, l'entreprise a décidé en 2017 de moderniser son système de planification, qui reposait encore beaucoup sur des fichiers Excel et des processus manuels. Elle lance alors le projet OSCAR. Celui-ci avait pour but d'accélérer la planification en intégrant mieux les différents métiers, notamment la teinture, mais aussi de fiabiliser les plans de production. En effet, près de 40% des plans fournis avant le projet n'étaient pas exécutables, notamment car certains composants manquaient. « Le projet voulait répondre à trois grands enjeux », détaille Christian Bouillot. « D'abord, augmenter le chiffre d'affaires, en améliorer le taux de service client et en limitant les ruptures d'approvisionnement. Ensuite, réduire les stocks en cours de saison pour diminuer les coûts. Enfin, augmenter la rentabilité, en diminuant les stocks résiduels de fin de saison, en accroissant la réactivité et en améliorant la productivité des usines. »
Pour ce projet, Petit Bateau a décidé de mettre en place la solution de FuturMaster. Après une première rencontre sur un salon, l'entreprise avait en effet apprécié la cohérence de celle-ci par rapport à ses problématiques, notamment sa prise en compte des différents niveaux de la supply chain. Un Proof of Concept a également permis au préalable de valider l'adéquation de la solution avec les besoins. Dans le cadre du projet OSCAR, la solution sert à planifier la production sur les différents sites et métiers concernés. Elle fournit les plans de production et permet de gérer les transferts de matières d'un site à l'autre. Oscar est alimenté par un plan d'approvisionnement par entrepôt, comportant des dates et quantités pour chaque référence coloris/taille de la collection en cours. « La solution distingue les besoins fermes, destinés aux implantations, des besoins non fermes, pour les réassorts », indique Christian Bouillot. Les besoins non fermes ont pour but d'éclairer sur les besoins futurs en capacités et matières. Ils sont transformés en besoins fermes au fil de l'eau, en se basant sur la connaissance du client. « Cela nous évite ainsi de lancer la fabrication de produits que nous ne sommes pas sûrs de pouvoir vendre. » Le système ERP SAP fournit également des données à FuturMaster, notamment des données techniques, des nomenclatures ou des données sur les stocks. A partir de ces données, le système de planification applique différentes règles de gestion, comme des priorités de production ou des répartitions de charge par site, des scénarios de production au plus tôt / au plus tard, ainsi que différentes contraintes (capacités de production, affectations produits, tailles de lot, quantité minimum, etc.). Cela lui permet de proposer en sortie des plans de production et de transfert « exécutables et réalistes » selon Christian Bouillot. Ces plans sont ensuite déversés dans SAP, qui prend le relais opérationnel et pilote leur mise en oeuvre.
Des stocks réduits et une productivité accrue
Grâce au projet, Petit Bateau a réussi à raccourcir la durée du processus de planification de 13 à 7 jours, réduisant ainsi le time-to-market de 6 jours. « Nous avons un cycle de planification hebdomadaire », explique Christian Bouillot. « Les données sont intégrées le week-end pour une première planification le lundi, qui exprime le besoin idéal, autrement dit celui exprimé par le client, sans prendre en compte à ce stade les notions de capacités. Les deux jours suivants, nous planifions les besoins de tricotage, en incluant les paramètres de capacité et de disponibilité des matières, les stocks de produits semi-finis, les encours... Cela nous permet d'obtenir dès mercredi soir un plan de production réalisable et qui répond le mieux possible au besoin du client ». Ce plan est ensuite repris dès jeudi pour établir un plan de confection. « Une prévision rentrée le vendredi soir est exécutée le week-end suivant », illustre Christian Bouillot. Hormis la réduction des délais, le projet a également renforcé la fiabilité des plans de production, permettant des gains de performance à tous les niveaux. L'entreprise estime ainsi avoir augmenté de 1% la productivité de son usine de Tenmar, bénéfice démultiplié quand il faut gérer plusieurs niveaux de production. Les stocks en cours ont été réduits d'une semaine, et les stocks résiduels, toutes matières confondues, de 6%. Enfin, les équipes chargées de la planification ont également accru leur productivité, mettant à profit le temps économisé pour faire davantage de travail d'analyse et d'optimisation. Parmi les facteurs qui ont contribué à la réussite du projet, Jean-Philippe Gauthier souligne notamment le rôle de la qualité des données, dont dépend directement la fiabilité du résultat final.
L'entreprise envisage aujourd'hui d'étendre la planification pour mieux prendre en compte les besoins en matières premières, afin d'anticiper les risques qui portent sur les approvisionnements en composants et fournitures. « OSCAR nous apporte la possibilité de réquisitionner les fournitures au bon moment et dans les bonnes quantités, afin de pouvoir produire au moment adéquat et d'éviter ainsi des ruptures dans la chaîne », explique Christian Bouillot. Réduire les cycles de planification d'une semaine permet également d'accélérer la prise de décision, ce qui contribue également à faire diminuer les stocks en excès et les ruptures d'approvisionnements. Le projet favorise ainsi une meilleure adéquation entre les approvisionnements et la demande, réduisant le gaspillage. Pour aller plus loin dans sa démarche, l'entreprise réfléchit désormais sur l'économie circulaire, expérimentant actuellement un dispositif de collecte des produits déjà portés pour les remettre en vente. Elle travaille également sur l'intégration de fibres recyclées dans ses produits.
Article rédigé par

Aurélie Chandeze, Rédactrice en chef adjointe de CIO
Suivez l'auteur sur Linked In,
Commentaire
INFORMATION
Vous devez être connecté à votre compte CIO pour poster un commentaire.
Cliquez ici pour vous connecter
Pas encore inscrit ? s'inscrire